Lessons Learned Working in a Resource Constrained Environment
- Ashley Martin
- Dec 3, 2017
- 4 min read
Living and working in Haiti the past month has already taught me so much. The difficulties and realities of operating in a place where resources are extremely limited has not only challenged me, but pushed me to become a better engineer. As a little background, while I am here in Haiti, I will be completing research involving chlorination techniques of the local water system in the village of Cange designed by engineers in the 1980s and updated with the help of Clemson engineers in the recent years. What sounded simple enough, however, became a much larger challenge when the lids of the brand new chlorinator we installed blew off the top after just a week of use, rendering the whole machine useless. So much more was at stake than just my research project when the second lid was damaged as this is the only potable water source the people living here have and the chlorine in the water is part of what makes it safe to drink and prevents people from getting waterborne diseases that are prevalent in Haiti. After speaking with David Vaughn, the Program Director of Clemson Engineers for Developing Countries, over the phone, my partner, Alex Arzon and I knew we would have to find a solution as soon as possible as getting new caps would take at least a week and when dealing with drinking water, there’s no time to waste. We also knew in the back of our minds that after we solved the immediate problem, we would have to find a way to keep it from happening again once the new caps arrived. Spoiler alert: we managed to fix both problems despite being in a resource constrained environment and here are few of the lessons I took away from the experience.

Be Creative: Most of the time, the closest stores to us that have what we would need to make a repair such as this one are located in Haiti’s capital, Port-au-Prince, which is a 2+ hour drive away from us. Because time was of the essence, spending that much time going to get parts was not an option and we knew we would have to get creative and use what we had on hand. We went through the cycle of determining what materials we had here in Cange, getting an idea, laying out piping, realizing we didn’t have everything we needed for the plan to work, and going back to the drawing board and starting over a couple of times. Staying focused, positive, and open minded were important as it could be frustrating at times thinking that nothing would work. Finally, we thought of a solution and assembled our local water team of technicians to help us install the “Nouvo, Nouvo Machin Klorox,” or “New, New Chlorinator” as it has been named since the name of “New Chlorinator” was already taken by the one we had installed a week earlier.

It Doesn’t Have to be Ideal, it Just Has to Work: Over the next few hours, we worked together to take apart old piping in the system and place in our new, very simple solution. It consisted of PVC piping tied in to the existing galvanized line with a T fitting and a ball valve in the middle for chlorine tablets to be dropped down into the piping. Only opening the surrounding ball valves a tiny amount allows some of the water to pass through and be chlorinated by the tablets – like in an erosion chlorinator – before mixing in with the remainder of the unchlorinated water. It wasn’t perfect, or pretty (the things I love most about good engineering design), but it worked and that was the only important thing in that moment. We were able to see almost instant results in the system as chlorine levels began to rise.
Be Flexible: After the temporary solution was in place, we set out to solve the next problem on our agenda – How do we keep this from happening again. We decided it would be best to install pressure relief valves
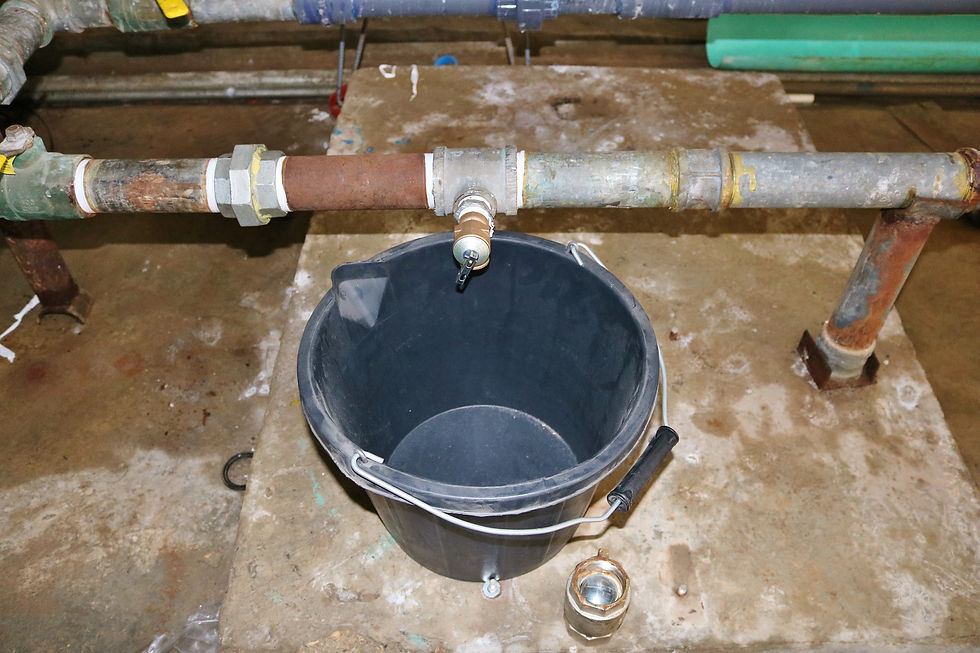
on either side of the chlorinator in order to keep the pressure from rising high enough to break the caps off again after they were replaced. We made a list of everything we would need to install the valves and when we got to Port-au-Prince, we could only find about half of it. We traveled to three hardware stores before we were even able to find pressure relief valves and we bought the only two the store had left. We made adjustments to the rest of our list based on what we could find and were on our way.
Since then, we have installed the pressure relief valves and have gotten the replacement caps for the chlorinator. So far, there have been no problems with using the original chlorinator and it is working just as it was designed to do. While at times this process was a headache to deal with, I learned so much working through it and truly enjoyed the challenge it presented. At the end of the day, that’s what engineers do no matter what environment they may find themselves in: face challenges and find solutions.
Comments